This article considers the effects of DC components in non-linear circuits₁ and their impact when induced in the ferromagnetic core of an RCD.
The effects of magnetic hysteresis for different types of RCD will also be considered.
An RCD is typically constructed from coils of wire wound around a toroidal ferrite core, one for each live conductor of the circuit protected. In a linear circuit with resistive loads the magnetic flux induced in the core by the currents flowing in both conductors is equal and in opposite directions; they subsequently cancel out and hence, no current will be induced in the trip coil.
However, where an earth fault exists, the current flow in both conductors is no longer equal in magnitude. Consequently, the magnetic flux induced in the magnetic core is no longer cancelled out.
This magnetic flux links with the search coil and induces an emf in it and, subsequently, a small current will flow into the tripping circuit operating the tripping coil and opening the contacts of the RCD, thereby isolating the faulty circuit (see Fig 1).

Consider an AC supply connected to a coil wound on a magnetically soft iron core, as shown in Fig 2.
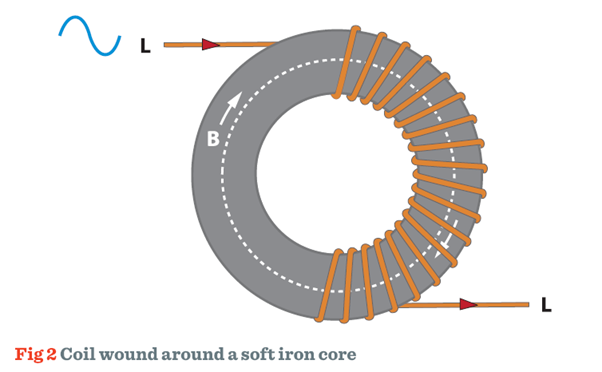
During the cycling period of the AC supply there is a constant change in the direction of the flow of current and consequently a reversal in the polarity of the resultant magnetic flux (B) induced in the core. This allows magnetisation in one direction, then demagnetisation, and again, magnetisation in the opposite direction.
Typically, the magnetic material used for the core will require time to adapt to these changes in direction of the magnetic flux such that the magnetic induction taking place within the ferromagnetic material lags behind the applied current and external magnetising force (H), as shown by the B-H curve (see Fig 3) which forms the hysteresis loop.
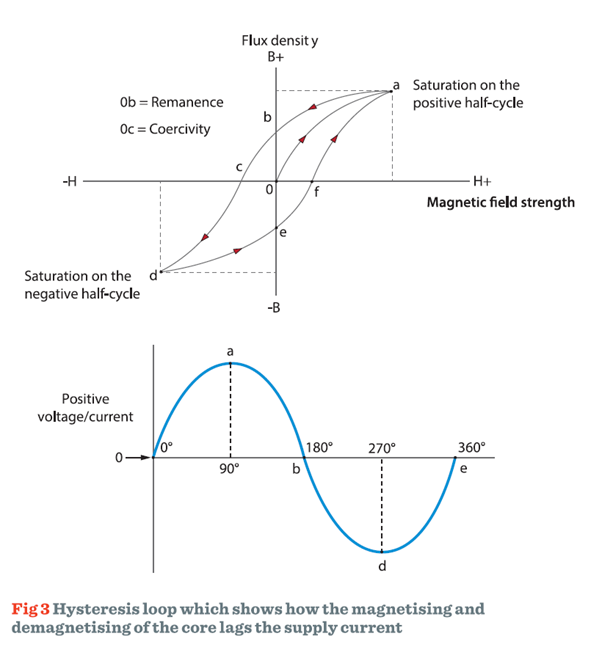
With reference to Fig 3,
• Curve (a - b): the supply current to the coil (magnetising force) has started to fall towards zero, an alternative path is taken from that of the initial magnetising curve, point (0 - a). When the current in the coil reaches zero, there is still some magnetic flux density remaining in the core. This is called the 'remanence'. The value of residual magnetic flux remaining within the core is usually determined by the type and quality of material used₂ (see Fig 4).
• Curve (b - c): the supply current is now moving into its negative half-cycle. Notice that more current is required to force the magnetic material to the point where it is no longer magnetic. This point (c), it is termed the point of 'coercivity'.
• With the continuing flow of reverse current, the magnetising force continues to increase in the negative direction towards point (d) and magnetic saturation again occurs. Then, as before, the flow of current in the negative direction approaches zero on the x-axis, which in turn, reduces the magnetising force and the flux density to point (e) in the loop, such that, the AC current is subsequently at (0).
• Similarly, a residual flux remains within the core at curve (e - f) until gradually removed by the magnetising force and current flowing in the positive direction of the subsequent supply waveform.
• Notice that the hysteresis loop is symmetrical. This loop continues endlessly for as long as the supply is connected. The area of the loop is a measure of the loss. The larger the area of the hysteresis loop, then the larger the loss; conversely, the smaller the area the smaller the loss.
Unlike linear connected loads, final circuits containing equipment with passive and active electronic components, typically used for high frequency switching during the conversion of an DC to AC supply for example, can produce complex waveforms that contain smaller currents at higher frequencies₃. As a result, the operational currents can impose changes in the impedance of the equipment with respect to the applied voltage.
In such cases, the resultant load and earth leakage residual currents will likely comprise pulsed and/ or smooth DC components as an operational characteristic of the connected equipment, and not only under fault conditions₄.
At this point, any current having a forward bias DC component would typically be induced into the toroid core of the RCD. Depending on the magnitude of the direct current, this may result in a relatively small residual flux, or alternatively, an increasing flux within the RCD core, reaching the point of saturation and full magnetisation as described earlier in this article.
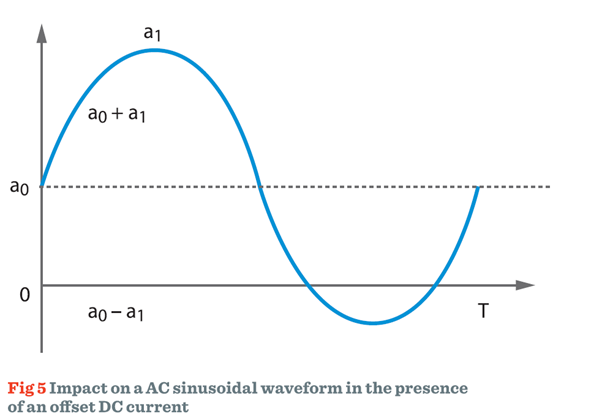
Although it is recognised that multiple waveforms are present in such circumstances, Fig 5, provides an example of a single AC sinusoidal residual current waveform (a₁) superimposed on an existing DC component (a₀). This shift represents a greater proportion of the AC current waveform offset in a positive direction on the Y-axis. This further increases saturation in the core and consequently, changes the operating point of the magnetic material as shown on the (H) axis in Fig 6 (ii).
It is worth noting at this point that the magnitude of both positive and negative cycles of the residual current remain the same; it is, however, the complete AC waveform that is offset by the presence of the DC current.
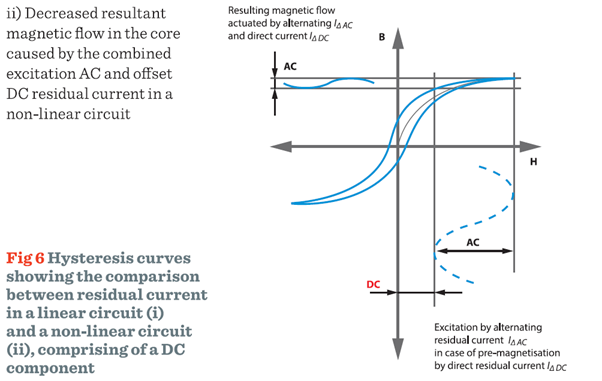
Such conditions can have a detrimental effect on the sensitivity and functionality of an RCD. Any subsequent leakage fault current to earth could go undetected, as it may no longer be possible for the AC residual current and resultant magnetising force to impose any further changes in the direction of the magnetising flux within the ferromagnetic material, due to the pre-existing core saturation caused by the direct residual current (I∆DC). Therefore, very little or no emf would be induced in to the coil and trip circuit. In effect, the core has become saturated to a point where the search coil cannot detect an emf (see Fig 6 (ii)).
This is sometimes referred to as "RCD blinding", because of the persistent remanence₅.
Note: Historically some test equipment manufacturers used artificial core saturation to provide an RCD 'No-Trip' function while an earth loop impedance test was carried out.
It should be recognised that some manufacturers produce microprocessorcontrolled RCDs that have a selfdiagnostic facility and are able to continually monitor for DC components more accurately and verify the status of DC fault currents.
Also considered were the effects of the DC component when imposed in the core of an RCD due to the presence of active and passive semiconductors in nonlinear loads.
The characteristics of magnetic material used within the toroid core of Type AC and Type A RCDs was also considered.
***
1. A non-linear circuit is an electrical circuit whose parameters (for example, resistance, inductance, and frequency) are varied with respect to voltage and current. A non-linear circuit would include such components as diodes, transistors, transformers and the like. The output waveform would not be represented by a straight line (linear) but a curve.
2. The material used within the primary magnetic circuit (B/H curve) of an A Type RCD will typically have improved characteristics over that used for an AC type. The core material must be able to withstand the DC component to prevent early core saturation.
3. Annex 53 and Figure A53.1 of BS 7671 provides some examples of the irregular waveforms resulting from such types of equipment containing semiconductors and identifies how the shape of the waveform is affected for various types of connected loads under fault conditions.
4. Higher and mixed frequency components may also exist depending on the type of connected loads, although this is outside the scope of this article.
5. Remanence is the flux density (magnetism) retained in material once the point of saturation has been reached and the external magnetising force has been removed.
Introduction
The fundamental principles for the operation of an RCD have long been recognised when used for monitoring earth leakage current in a circuit.An RCD is typically constructed from coils of wire wound around a toroidal ferrite core, one for each live conductor of the circuit protected. In a linear circuit with resistive loads the magnetic flux induced in the core by the currents flowing in both conductors is equal and in opposite directions; they subsequently cancel out and hence, no current will be induced in the trip coil.
However, where an earth fault exists, the current flow in both conductors is no longer equal in magnitude. Consequently, the magnetic flux induced in the magnetic core is no longer cancelled out.
This magnetic flux links with the search coil and induces an emf in it and, subsequently, a small current will flow into the tripping circuit operating the tripping coil and opening the contacts of the RCD, thereby isolating the faulty circuit (see Fig 1).
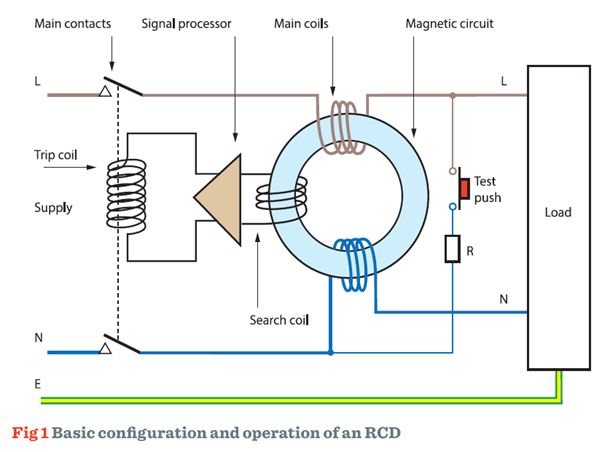
Hysteresis overview
Hysteresis in a magnetic material means the lagging behind of the magnetic flux with respect to the current causing it. This will be explained further in the article.Consider an AC supply connected to a coil wound on a magnetically soft iron core, as shown in Fig 2.
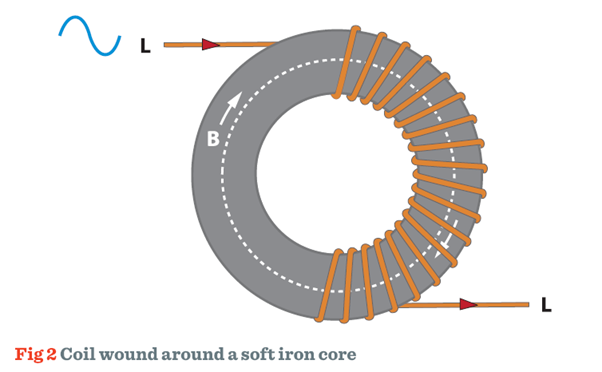
During the cycling period of the AC supply there is a constant change in the direction of the flow of current and consequently a reversal in the polarity of the resultant magnetic flux (B) induced in the core. This allows magnetisation in one direction, then demagnetisation, and again, magnetisation in the opposite direction.
Typically, the magnetic material used for the core will require time to adapt to these changes in direction of the magnetic flux such that the magnetic induction taking place within the ferromagnetic material lags behind the applied current and external magnetising force (H), as shown by the B-H curve (see Fig 3) which forms the hysteresis loop.
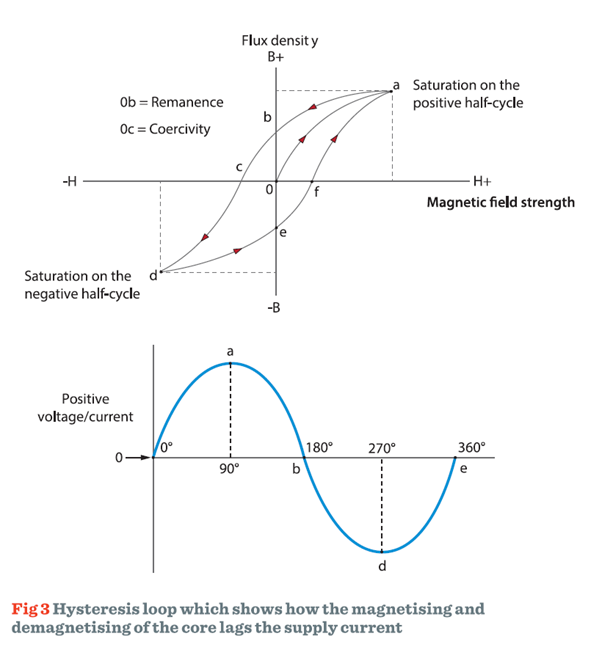
With reference to Fig 3,
• Curve (a - b): the supply current to the coil (magnetising force) has started to fall towards zero, an alternative path is taken from that of the initial magnetising curve, point (0 - a). When the current in the coil reaches zero, there is still some magnetic flux density remaining in the core. This is called the 'remanence'. The value of residual magnetic flux remaining within the core is usually determined by the type and quality of material used₂ (see Fig 4).
• Curve (b - c): the supply current is now moving into its negative half-cycle. Notice that more current is required to force the magnetic material to the point where it is no longer magnetic. This point (c), it is termed the point of 'coercivity'.
• With the continuing flow of reverse current, the magnetising force continues to increase in the negative direction towards point (d) and magnetic saturation again occurs. Then, as before, the flow of current in the negative direction approaches zero on the x-axis, which in turn, reduces the magnetising force and the flux density to point (e) in the loop, such that, the AC current is subsequently at (0).
• Similarly, a residual flux remains within the core at curve (e - f) until gradually removed by the magnetising force and current flowing in the positive direction of the subsequent supply waveform.
• Notice that the hysteresis loop is symmetrical. This loop continues endlessly for as long as the supply is connected. The area of the loop is a measure of the loss. The larger the area of the hysteresis loop, then the larger the loss; conversely, the smaller the area the smaller the loss.
RCDs
Some RCD manufacturers refer to hysteresis loops within their technical data. As shown in Fig 4, hysteresis loops vary for the different operating characteristics of RCDs, typically due to the magnetic properties of the material used for the toroid core. A Type AC RCD core generally employs a magnetically harder material. This produces greater energy losses, has a higher remanence and retains a greater proportion of magnetic flux long after the external force is removed than a magnetically softer core would. Type A RCDs employ a magnetically softer material core producing less energy losses with a lower remanence in which a much smaller proportion of magnetic flux is retained (see Fig 4 (b)).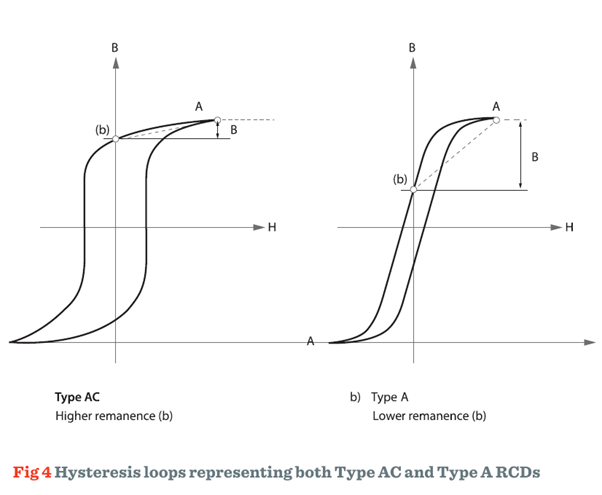
Non-linear loads
Equipment such as static inverters used in solar PV and battery energy storage systems, and variable frequency drives are typical examples of non-linear loads.Unlike linear connected loads, final circuits containing equipment with passive and active electronic components, typically used for high frequency switching during the conversion of an DC to AC supply for example, can produce complex waveforms that contain smaller currents at higher frequencies₃. As a result, the operational currents can impose changes in the impedance of the equipment with respect to the applied voltage.
In such cases, the resultant load and earth leakage residual currents will likely comprise pulsed and/ or smooth DC components as an operational characteristic of the connected equipment, and not only under fault conditions₄.
At this point, any current having a forward bias DC component would typically be induced into the toroid core of the RCD. Depending on the magnitude of the direct current, this may result in a relatively small residual flux, or alternatively, an increasing flux within the RCD core, reaching the point of saturation and full magnetisation as described earlier in this article.
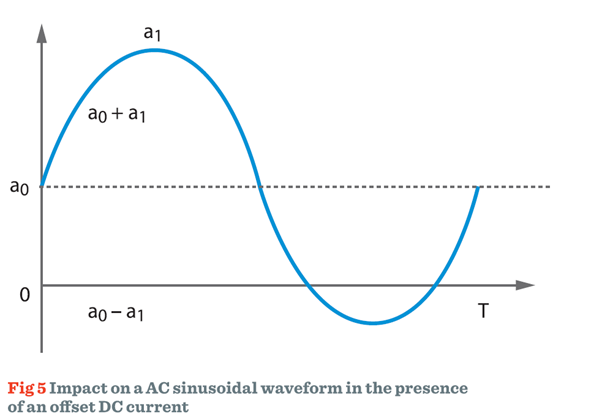
Although it is recognised that multiple waveforms are present in such circumstances, Fig 5, provides an example of a single AC sinusoidal residual current waveform (a₁) superimposed on an existing DC component (a₀). This shift represents a greater proportion of the AC current waveform offset in a positive direction on the Y-axis. This further increases saturation in the core and consequently, changes the operating point of the magnetic material as shown on the (H) axis in Fig 6 (ii).
It is worth noting at this point that the magnitude of both positive and negative cycles of the residual current remain the same; it is, however, the complete AC waveform that is offset by the presence of the DC current.
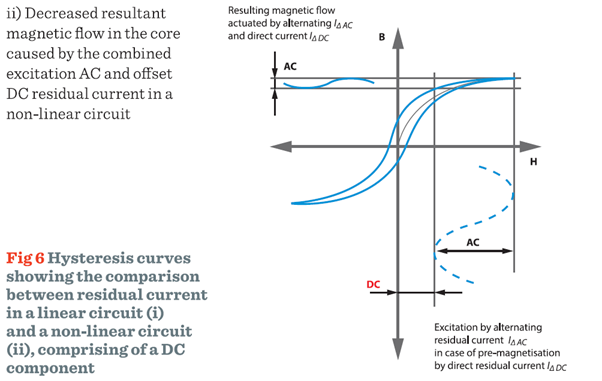
Such conditions can have a detrimental effect on the sensitivity and functionality of an RCD. Any subsequent leakage fault current to earth could go undetected, as it may no longer be possible for the AC residual current and resultant magnetising force to impose any further changes in the direction of the magnetising flux within the ferromagnetic material, due to the pre-existing core saturation caused by the direct residual current (I∆DC). Therefore, very little or no emf would be induced in to the coil and trip circuit. In effect, the core has become saturated to a point where the search coil cannot detect an emf (see Fig 6 (ii)).
This is sometimes referred to as "RCD blinding", because of the persistent remanence₅.
Note: Historically some test equipment manufacturers used artificial core saturation to provide an RCD 'No-Trip' function while an earth loop impedance test was carried out.
It should be recognised that some manufacturers produce microprocessorcontrolled RCDs that have a selfdiagnostic facility and are able to continually monitor for DC components more accurately and verify the status of DC fault currents.
Summary
This article looked at the fundamental principles of an RCD while providing an overview of the hysteresis loop.Also considered were the effects of the DC component when imposed in the core of an RCD due to the presence of active and passive semiconductors in nonlinear loads.
The characteristics of magnetic material used within the toroid core of Type AC and Type A RCDs was also considered.
***
1. A non-linear circuit is an electrical circuit whose parameters (for example, resistance, inductance, and frequency) are varied with respect to voltage and current. A non-linear circuit would include such components as diodes, transistors, transformers and the like. The output waveform would not be represented by a straight line (linear) but a curve.
2. The material used within the primary magnetic circuit (B/H curve) of an A Type RCD will typically have improved characteristics over that used for an AC type. The core material must be able to withstand the DC component to prevent early core saturation.
3. Annex 53 and Figure A53.1 of BS 7671 provides some examples of the irregular waveforms resulting from such types of equipment containing semiconductors and identifies how the shape of the waveform is affected for various types of connected loads under fault conditions.
4. Higher and mixed frequency components may also exist depending on the type of connected loads, although this is outside the scope of this article.
5. Remanence is the flux density (magnetism) retained in material once the point of saturation has been reached and the external magnetising force has been removed.